Categories
General
Thermocouple Types
- Thermocouple Types
- Thermocouple Wire Types
- Thermocouple Wire Colors
- US ANSI Thermocouple Color Codes for Each Type of Thermocouple
- Type K Thermocouple (Nickel Chromium/ Nickel-Alumel)
- Type J Thermocouple (Iron/Constantan)
- Type T Thermocouple (Copper Constantan)
- Type E Thermocouple (Nickel-Chromium/Constantan)
- Type N Thermocouple (Nicrosil/Nisil)
- Noble Metal Thermocouples (Type S, R &B)
Thermocouple Accuracy
Thermocouple Construction
- Thermocouple Junction Types
- Mineral Insulated Cable
- Maximum Lead Wire Length
- Wire Length Guide
- Thermocouple Sheath Material
Thermocouple Temperature Ranges/Limits
General
Thermocouples Explained
A thermocouple is a sensor used to measure temperature. Thermocouples consist of two wire legs made from different metals. The wire legs are welded together at one end, creating a junction. This junction is where the temperature is measured. When the junction experiences a change in temperature, a temperature dependant voltage is produced. The voltage can then be interpreted using thermocouple reference tables to calculate the temperature.
There are many types of thermocouples, each with their own unique characteristics in terms of temperature range, chemical resistance, and application compatibility. Type J, K, T, & E are “Base Metal” thermocouples, the most common type of thermocouple. Type R, S, and B thermocouples are “Noble Metal” thermocouples (due to high platinum content), which are used in high temperature applications (see thermocouple temperature ranges for more details).
Thermocouples are used in many industrial, scientific, and OEM applications. They can be found in nearly all industrial markets: Power Generation, Oil/Gas, Pharmaceutical, Biotech, Cement, Paper & Pulp, etc. Thermocouples are also used in everyday appliances like stoves, furnaces, and toasters.
Thermocouples are typically selected because of their low cost, high temperature limits, wide temperature ranges, and durable nature.
Thermocouples vs. RTDs
Temperature Range: First, consider the difference in temperature ranges. Base metal thermocouples can reach 2,300°F and noble metal thermocouples can reach 3,100°F. Compare this to RTDs which have a standard maximum range of 400°F and an extended maximum range of 1,100°F.
Cost: A thermocouple has lower initial cost compared to an equivalent RTD unit.
Accuracy, Linearity, & Stability: As a general rule, RTDs are more accurate than thermocouples. This is especially true at lower temperature ranges. RTDs are also more stable and have better linearity than thermocouples. If accuracy, linearity, and stability are your primary concerns and your application is within an RTD’s temperature limits, go with the RTD.
Durability: In the sensors industry, RTDs are widely regarded as a less durable sensor when compared to thermocouples. However, Reotemp has developed manufacturing techniques that have greatly improved the durability of our RTD sensors. These techniques make Reotemp’s RTDs nearly equivalent to thermocouples in terms of durability.
Response Time: RTDs cannot be grounded. For this reason, they have a slower response time than grounded thermocouples. Also, thermocouples can be placed inside a smaller diameter sheath than RTDs. A smaller sheath diameter will reduce response time. For example, a grounded thermocouple inside a 1/16” diameter sheath will have a faster response time than a RTD inside a ¼” diameter sheath. The effect of sheath diameter on thermocouple response time, for both grounded and ungrounded, is shown in the chart on page 6.
Hazardous Locations or Applications
Safety is a primary concern when instruments are used in hazardous locations, especially in applications where the potential for explosion is involved due to a concentration of flammable gases, vapors or dust. When specifying a sensor or any instrumentation circuit for use in a hazardous location, the user needs to exercise caution in complying with local and/or national electrical codes and safety regulations.
It is important to consider the failure modes of the instrumentation and any catastrophic effects these modes could have based on the environment they are used in. The integrity and suitability of any instrumentation for use in hazardous locations is ultimately the responsibility of the end user and/or of those making the specification decisions.
Generally, when instrumentation is to be used in a hazardous location, two commonly used methods to minimize the risk of ignitions and explosions are intrinsically safe and explosion-proof systems. Intrinsically safe systems are centered around prevention whereas explosion proof systems are focused on containment.
Intrinsically safe systems operate on low power and are designed to limit the thermal and electrical energy of the instrument and associated connections to a level where ignition is not possible. Also, the devices cannot store enough energy to cause a spark when energy is released.
Explosion proof systems are based on the principle of containment. In other words, an explosion proof enclosure prevents any generated flames, sparks or hot gases from escaping. These devices are designed to contain, control, cool, and/or vent any possible ignition due to a failure mode, without igniting the surrounding atmosphere.
When it comes to RTDs and thermocouples, it is important to note that these temperature measurement sensors are defined as simple apparatus by the National Fire Protection Association (NFPA). This means that they simply operate on, store and/or generate too low level an energy, i.e. low amperage and low voltage, to cause an ignition. This status can change, however, depending on what the sensor is connected to or how hot the surface of the sensor assembly may get outside of the process. The required method of protection can vary depending on many different factors and the entire instrumentation system must be examined before use in hazardous locations.
In summary, RTD and thermocouple sensors are considered a simple apparatus as defined in the National Electric Code NFPA 70 Article 100 (Rev. 2020). By definition, these sensors generate too low an energy to be an ignition source. For use in hazardous environments, the sensor is typically connected to an intrinsically safe or explosion proof apparatus. Final application suitability and compliance with regional standards are to be determined and approved by the end user.
Thermocouple Types
There are multiple types and grades of thermocouple. Each type of thermocouple wire has a specific combination of metal alloys. This combination is what defines the type of thermocouple. For example, a type K thermocouple is made when a wire of Nickel-Chromium is welded to a wire of Nickel-Aluminium. The grade of the thermocouple is dependent not only on the combination of alloys used, but also on the purity of those alloys. Learn more on our thermocouple wire FAQ page.
This chart shows each thermocouple type and its estimate millivolt output vs temperature. Note that the color codes on this page refer to the United States ANSI MC96.1 1982 colors, a chart of US ANSI color codes see our wire FAQ page.
Thermocouple Wire Types
There are multiple types and grades of thermocouple wire. Each type of thermocouple wire has a specific combination of metal alloys. This combination is what defines the type of thermocouple. For example, a type K thermocouple is made when a wire of Nickel-Chromium is welded to a wire of Nickel-Alumel. The grade of the wire is dependent not only on the combination of alloys used, but also on the purity of those alloys.
For a full list of thermocouple types and corresponding thermocouple wires, see our thermocouple types page. For a full selection of Reotemp products featuring thermocouples visit the thermocouple landing page.
Type K Thermocouple (Nickel Chromium / Nickel-Alumel)
Type K Thermocouple (Nickel-Chromium / Nickel-Alumel) is the most common type of thermocouple. It’s inexpensive, accurate, reliable, and has a wide temperature range. The type K is commonly found in nuclear applications because of its relative radiation hardness. Maximum continuous temperature is around 1,100°C.
Type K Temperature Range | |
---|---|
Thermocouple Grade Wire | –328°F to 2,300°F |
Extension Wire | 32°F to 392°F |
Type K Accuracy | |
---|---|
Standard | +/- 2.2°C or +/- .75% |
Special Limits of Error | +/- 1.1°C or 0.4% |
Type J Thermocouple (Iron/Constantan)
Type J Thermocouple (Iron/Constantan) is also very common. It has a smaller temperature range and a shorter lifespan at higher temperatures than the Type K. It is equivalent to the Type K in terms of expense and reliability. Consideration for bare wire Type J thermocouple applications: the Type J is well suited to oxidizing atmospheres.
Type J Temperature Range | |
---|---|
Thermocouple Grade Wire | 32°F to 1,400°F |
Extension Wire | 32°F to 392°F |
Type J Accuracy | |
---|---|
Standard | +/- 2.2°C or +/- .75% |
Special Limits of Error | +/- 1.1°C or 0.4% |
Thermocouple Wire Colors
A thermocouple can be identified by the color of its wire insulation. For example, in the United States a type J thermocouple grade wire has one red wire and one white wire, typically with a brown over jacket. A type J extension grade wire also has one red wire and one white wire, but it has a black over jacket. As a general rule the red wire of a thermocouple or extension wire is negative and the positive wire is color coded according to the type of thermocouple. Different countries use different color codes.
Type T Thermocouple (Copper/Constantan)
Type T Thermocouple (Copper/Constantan) is a very stable thermocouple and is often used in extremely low temperature applications such as cryogenics or ultra low freezers. Consideration for bare wire type T thermocouple applications: The Type T Is Well Suited To Oxidizing Atmospheres.
Type T Temperature Range | |
---|---|
Thermocouple Grade Wire | –328°F to 700°F |
Extension Wire | 32°F to 392°F |
Type T Accuracy | |
---|---|
Standard | +/- 1.0°C or +/- .75% |
Special Limits of Error | +/- 0.5°C or 0.4% |
Type E Thermocouple (Nickel-Chromium/Constantan)
The Type E has a stronger signal & higher accuracy than the Type K or Type J at moderate temperature ranges of 1,000°F and lower. The type E is also more stable than the type K, which adds to its accuracy. Consideration for bare wire type E thermocouple applications: In oxidizing or inert atmospheres the operating range is roughly –418°F to 1,652°F (–250°C to 900°C).
Type E Temperature Range | |
---|---|
Thermocouple Grade Wire | –328°F to 1,600°F |
Extension Wire | 32°F to 392°F |
Type E Accuracy | |
---|---|
Standard | +/- 1.7°C or +/- 0.5% |
Special Limits of Error | +/- 1.0°C or 0.4% |
Type N Thermocouple (Nicrosil/Nisil)
The Type N shares the same accuracy and temperature limits as the Type K. The type N is slightly more expensive. Consideration for bare wire type N thermocouple applications: The type N holds up better to oxidation at high temperatures when compared to the type K.
Type N Temperature Range | |
---|---|
Thermocouple Grade Wire | 32°F to 2,300°F |
Extension Wire | 32°F to 392°F |
Type N Accuracy | |
---|---|
Standard | +/- 2.2°C or +/- 0.75% |
Special Limits of Error | +/- 1.1°C or 0.4% |
Noble Metal Thermocouples (Type S, R & B)
Noble Metal Thermocouples are selected for their ability to withstand extremely high temperatures while maintaining their accuracy and lifespan. They are considerably more expensive than Base Metal Thermocouples.
Type S Thermocouple (Platinum Rhodium 10%/Platinum)
The Type S is used in very high temperature applications. It is commonly found in the BioTech and Pharmaceutical industries. It is sometimes used in lower temperature applications because of its high accuracy and stability. Consideration for bare wire type S thermocouple applications: The Type S can be used in inert and oxidizing atmospheres up to 2,912F (1600C) continuously and up 3,092F (1,700C) for short term use.
Type S Temperature Range | |
---|---|
Thermocouple Grade Wire | 32°F to 2,700°F |
Extension Wire | 32°F to 392°F |
Type S Accuracy | |
---|---|
Standard | +/- 1.5°C or +/- 0.25% |
Special Limits of Error | +/- 0.6°C or 0.1% |
Type R Thermocouple (Platinum Rhodium 13%/Platinum)
The Type R is used in very high temperature applications. It has a higher percentage of Rhodium than the Type S, which makes it more expensive. The Type R is very similar to the Type S in terms of performance. It is sometimes used in lower temperature applications because of its high accuracy and stability. Type R has a slightly higher output and improved stability over the type S.
Type R Temperature Range | |
---|---|
Thermocouple Grade Wire | 32°F to 2,700°F |
Extension Wire | 32°F to 392°F |
Type R Accuracy | |
---|---|
Standard | +/- 1.5°C or +/- 0.25% |
Special Limits of Error | +/- 0.6°C or 0.1% |
Type B Thermocouple (Platinum Rhodium 30%/Platinum Rhodium 6%)
The Type B thermocouple is used in extremely high temperature applications. It has the highest temperature limit of all of the thermocouples listed above. It maintains a high level of accuracy and stability at very high temperatures. The type B has a lower output than the other noble metals (type R & type S) at temperatures below 1,112F (600C).
Type B Temperature Range | |
---|---|
Thermocouple Grade Wire | 1500°F to 3,100°F |
Extension Wire | 32°F to 212°F |
Type B Accuracy | |
---|---|
Standard | +/- 0.5% |
Special Limits of Error | +/- 0.25% |
What are the US ANSI thermocouple color codes for each type of thermocouple?
Thermocouple Accuracy
The accuracy of a thermocouple depends on many factors including but not limited to electrical interference and the purity of the metals used.
THERMOCOUPLE & RTD ACCURACIES | ||||||||
---|---|---|---|---|---|---|---|---|
Type K | Type J | Type T | Type E | Type N | Type S | Type R | Type B | |
-328°F | * | – | * | * | – | – | – | – |
-148°F | * | – | * | * | – | – | – | – |
32°F | ± 3.96°F | ± 3.96°F | ± 1.8°F | ± 3.06°F | ± 3.96°F | ± 2.7°F | ± 2.7°F | – |
392°F | ± 3.96°F | ± 3.96°F | ± 2.7°F | ± 3.06°F | ± 3.96°F | ± 2.7°F | ± 2.7°F | – |
752°F | ± 5.4°F | ± 5.4°F | – | ± 3.6°F | ± 5.4°F | ± 2.7°F | ± 2.7°F | – |
1112°F | ± 8.1°F | ± 8.1°F | – | ± 5.4°F | ± 8.1°F | ± 2.7°F | ± 2.7°F | – |
1472°F | ± 10.8°F | – | – | ± 7.2°F | ± 10.8°F | ± 3.6°F | ± 3.6°F | – |
1832°F | ± 13.5°F | – | – | – | ± 13.5°F | ± 4.5°F | ± 4.5°F | ± 9°F |
2192°F | ± 16.2°F | – | – | – | ± 16.2°F | ± 5.4°F | ± 5.4°F | ± 10.8°F |
2552°F | – | – | – | – | – | ± 6.3°F | ± 6.3°F | ± 12.6°F |
2912°F | – | – | – | – | – | – | – | ± 14.4°F |
Note: The accuracies in the above table are estimates given at fixed points, they do not apply to temperature ranges and are intended only as examples to give a general idea of what can be expected. Consult Reotemp if a specific accuracy is required or to confirm accuracies at any points not listed in the above table. *Thermocouples are normally supplied to meet the tolerances specified in the table for temperatures above 32°F. The same materials, however, may not fall within the tolerances for temperatures below 32°F. If materials are required to meet the tolerances stated for temperatures below 32°F, contact Reotemp sales. |
Thermocouple Conductor Type | Limits of Error (Whichever is Greater) | |
---|---|---|
Standard | Special | |
Type K | ±2.2°C or ±0.75% | ±1.1°C or ±0.4% |
Type T | ±1.0°C or ±0.75% | ±0.5°C or ±0.4% |
Type J | ±2.2°C or ±0.75% | ±1.1°C or ±0.4% |
Type N | ±2.2°C or ±0.75% | ±1.1°C or ±0.4% |
Type E | ±1.7°C or ±0.5% | ±1.0°C or ±0.4% |
Type S | ±1.5°C or ±0.25% | ±0.6°C or ±0.1% |
Type R | ±1.5°C or ±0.25% | ±0.6°C or ±0.1% |
Type B | ±0.5% | ±0.25% |
What are Special Limits of Error (SLE)? What are Standard Limits of Error?
Standard limits of Error: These thermocouples use standard “thermocouple grade” wire and make up the great majority of sensors.
Special Limits of Error: These thermocouples are made with a higher grade of thermocouple wire that is purer than standard wire, which increases their accuracy. They are more expensive than standard thermocouples.
System Error
System error is calculated by adding the accuracy of the temperature sensor (thermocouple) and the accuracy of the meter used to read the voltage signal together. For example, a Type K thermocouple has an accuracy of +/- 2.2°C at 50°C. The meter has an accuracy of +/- 1.0°C. That means the total system error is +/- 3.2°C at 50°C.
Thermocouple Construction
Thermocouple Junction Types
There are four types of thermocouple junctions: grounded, ungrounded exposed and ungrounded uncommon.
Grounded: A thermocouple is grounded when both thermocouple wires and the sheath are all welded together to form one junction at the probe tip. Grounded thermocouples have a very good response time because the thermocouple is making direct contact with the sheath, allowing heat to transfer easily. A drawback of the grounded thermocouple is that the thermocouple is more susceptible to electrical interference. This is because the sheath often comes into contact with the surrounding area, providing a path for interference.
Ungrounded: A thermocouple is ungrounded when the thermocouple wires are welded together but they are insulated from the sheath.
Exposed: A thermocouple is exposed when the thermocouple wires are welded together and are sticking out of an open probe tip. The response time is very quick, but exposed thermocouple wires are more prone to corrosion and degradation. Unless your application requires exposed junctions, this style is not recommended.
Ungrounded Uncommon: An ungrounded uncommon thermocouple consists of a dual thermocouple that is insulated from the sheath and each of the elements are insulated from one another.
Mineral Insulated Cable
Mineral insulated (M.I.) cable is used to create thermocouple probes. M.I. cable insulates thermocouple wires from one another and provides the metal sheath that surrounds them. M.I. cable has two (or four when duplex) thermocouple wires running down the middle of the sheath. The sheath contains highly compacted magnesium oxide to ensure the wires are properly insulated and separated. M.I. cable helps to protect the thermocouple wire from corrosion and electrical interference and provides probes with the greatest durability and service life. Learn more about our thermocouple sheath materials here.
Maximum Lead Wire Length
How long can RTD lead wire be? How long can thermocouple lead wire be? What about 4-20mA transmitter lead wire? Find out in this video.
Wire Length Guide
Actual maximum lead wire length is dictated by total loop resistance and the presence of electrical noise. Allowable loop resistance is dictated by the equipment used to measure the sensor’s signal. The tables below have been generated using assumptions of allowable loop resistance. Final determination of suitability rests with the customer. Green zones indicate estimated lead wire lengths that will allow the temperature sensor to still function properly with limited accuracy loss. The exact accuracy loss is dependent on a number of application specific factors.
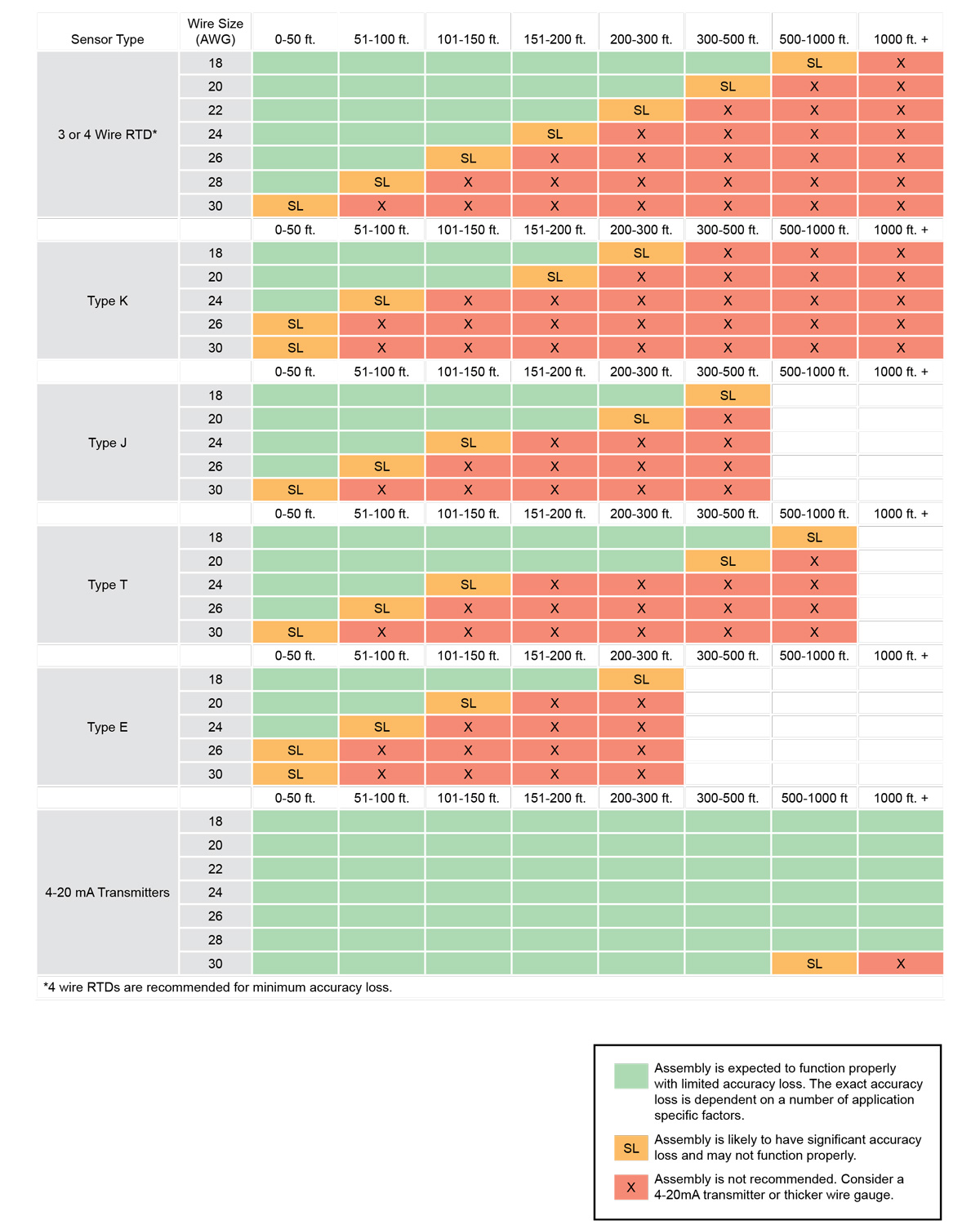
Thermocouple Sheath Material
A thermocouple is often enclosed in a protective sheath to isolate it from the local atmosphere. This protective sheath drastically reduces the effects of corrosion.
Specific Temperature Limits
316 Stainless Steel
- Maximum temperature: 1650°F(900°C). Best corrosion resistance of the austenitic stainless steel grades. Widely used in the food and chemical industry.
- Subject to damaging carbide precipitation in 900°F to 1600°F (482°C to 870°C).
316L Stainless Steel
- Maximum temperature: 1650°F (900°C). Same as 316 SST (04) except low carbon version allows for better welding and fabrication.
304 Stainless Steel
- Maximum temperature: 1650°F (900°C). Most widely used low temperature sheath material. Extensively used in food, beverage, chemical and other industries where corrosion resistance is required.
- Subject to damaging carbide precipitation in 900°F to 1600°F (480°C to 870°C) range. Lowest cost corrosion resistant sheath material available.
304L Stainless Steel
- Maximum temperature: 1650°F (900°C). Low carbon version of 304 SST (02). Low carbon content allows this material to be welded and heated in the 900°F to 1600°F (480°C to 870°C) range without damage to corrosion resistance.
310 Stainless Steel
- Maximum temperature: 2100°F (1150°C). Mechanical and corrosion resistance, similar to but better than 304 SS. Very good heat resistance.
- This alloy contains 25% chromium, 20% nickel. Not as ductile as 304 SS.
321 Stainless Steel
- Maximum temperature: 1600°F (870°C). Similar to 304 SS except titanium stabilized for intergranular corrosion.
- This alloy is designed to overcome susceptibility to carbon precipitation in the 900 to 1600°F (480 to 870°C) range. Used in aerospace and chemical applications.
446 Stainless Steel
- Maximum temperature: 2100°F (1150°C). Ferritic stainless steel which has good resistance to sulfurous atmospheres at high temperatures.
- Good corrosion resistance to nitric acid, sulfuric acid and most alkalies. 27% chromium content gives this alloy the highest heat resistance of any ferritic stainless steel.
Inconel 600
- Maximum temperature: 2150°F (1175°C). Most widely used thermocouple sheath material. Good high temperature strength, corrosion resistance, resistance to chloride-ion stress corrosion cracking and oxidation resistance to high temperatures.
- Do not use in sulfur bearing environments. Good in nitriding environments.
Inconel 601
- Maximum temperature: 2150°F (1175°C) continuous, 2300°F (1260°C) intermittent. Similar to Alloy 600 with the addition of aluminum for outstanding oxidation resistance. Designed for high temperature corrosion resistance.
- This material is good in carburizing environments, and has good creep rupture strength. Do not use in vacuum furnaces! Susceptible to intergranular attack by prolonged heating in 1000°F to 1400°F (540°C to 760°C) temperature range.
Incoloy 800
- Maximum temperature: 2000°F (1095°C). Widely used as heater sheath material. Minimal use in thermocouples. Superior to Alloy 600 in sulfur, cyanide salts and fused neutral salts.
- Susceptible to intergranular attack in some applications by exposure to the temperature range of 1000°F to 1400°F (540°C to 760°C).
Thermocouple Temperature Limits/Ranges
Thermocouple Temperature Limit Comparison
Thermocouple Temperature Operating Ranges | ||
---|---|---|
Type | Minimum Temp. °F | Maximum Temp. °F |
K | -328 | 2300 |
J | 32 | 1400 |
T | -328 | 700 |
E | -328 | 1600 |
N | 32 | 2300 |
S | 32 | 2700 |
R | 32 | 2700 |
B | 1600 | 3100 |
Specific Temperature Ranges for Thermocouples
Type K Thermocouple
- Thermocouple grade wire, –328°F to 2,300°F
- Extension wire, 32°F to 392°F
Type J Thermocouple
- Thermocouple grade wire, 32°F to 1,400°F
- Extension wire, 32°F to 392°F
Type T Thermocouple
- Thermocouple grade wire, -328°F to 700°F
- Extension wire, 32°F to 392°F
Type E Thermocouple
- Thermocouple grade wire, -328°F to 1600°F
- Extension wire, 32°F to 392°F
Type N Thermocouple
- Thermocouple grade wire, 32°F to 2300°F
- Extension wire, 32°F to 392°F
Type S Thermocouple
- Thermocouple grade wire, 32°F to 2700°F
- Extension wire, 32°F to 392°F
Type R Thermocouple
- Thermocouple grade wire, 32°F to 2700°F
- Extension wire, 32°F to 392°F
Type B Thermocouple
- Thermocouple grade wire, 1500°F to 3100°F
- Extension wire, 32°F to 212°F
Temperature Limits of Wire Jackets
Wire Jacket Limits | |
---|---|
Jacket | Temperature Limit |
PVC | 221°F |
Teflon | 400°F |
Fiberglass | 900°F |
Thermocouple Wire Cable vs. Extension Grade Wire
Thermocouple grade wire is used to manufacture thermocouple probes. Thermocouple grade wire is normally used for the junction and inside the stem sheath.
Extension grade wire is used to extend from the thermocouple probe to the control system or digital display. Extension grade wire is more economical due to lesser grade alloys being used. Extension grade wire is also not generally within the process and does not play as critical of a role as the thermocouple grade wire. It also does not experience the temperature extremes and cycling of the sensor itself.
In many industrial applications, a sensor is located in a process pipe far away from the control room. This means that wire must be run a considerable distance back to the control room to get the temperature reading. Using more expensive thermocouple grade wire to accomplish this is unnecessary. Extension grade wire will do the job.